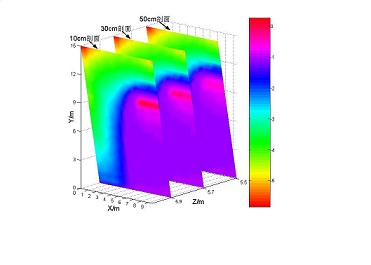
随着工业科技的发展,激光拼焊工艺在航天、航海、汽车、机械加工等行业中的应用越来越多。较之传统焊接工艺,通过激光拼焊工艺获得的拼焊板具有良好的冲压成形性能,并且其焊缝区体积小,拉伸强度较高。在生产汽车的车身时,通过激光拼焊技术可以减轻车身重量,提高冲压成型率和车身的机械结构性能。研究表明,焊缝的形状和焊缝区、HAZ(热影响区)的晶粒尺寸对拼焊板的抗拉强度、成形性能等有很大的影响。基于有限元分析软件对焊缝形状、晶粒大小进行预测,及时对焊接工艺做出调整和优化,可以实现对焊缝形状、晶粒大小的控制。因此本研究基于机械结构有限元分析,针对深冲钢拼焊板,创建了焊缝形状和晶粒大小的预测模型,并且进行了相关模拟,对于优化激光拼焊工艺具有十分重要的意义。
采用快速轴流CO2激光拼焊设备对St12、St16深冲钢激光拼焊板进行单面焊双面成形焊接。
焊缝与深冲钢板的轧制方向呈90°,沿压缩轴方向将模拟变形的试样从直径1/3处剖开,置入2%~4%HNO3溶液中进行腐蚀,制取金相试样。完成金相试样的制备后,使用光学显微镜观察其金相组织并进行分析。焊接试验中选用的深冲钢板尺寸为500mm×270mm×1.2mm。若对整体试件进行有限元建模,因计算量大、耗时长,使得建模较为困难,所以选取试件焊缝附近的一小块区域创建三维有限元模型,其中模型的热分析单元为Solid70,模型尺寸25mm×5mm×1.2mm。
焊缝形状具有较大的异样性,在模拟过程中会形成一定的系统误差,为了减小系统误差,在试件不同的区域进行不同疏密程度的网格划分,焊缝较远的区域,网格划分较为稀疏,焊缝和热影响区(HAZ)网格划分比较稠密,网格尺寸较小,为0.1mm×0.1mm×0.2mm,小于光斑直径。因焊缝平面具有对称性,只需建立单侧模型。
试验选用拼焊板厚度较薄(1.2mm),焊接时输出功率较小,所以确定为传导焊,热源模型为高斯热源模型。通过APDL编程的LOOP循环完成光源的移动,编程时设置100个载荷步实现热源的加载。为了令移动热源的加载符合实际的移动热源特性,需用重贴加载法进行加载即每进行完一步载荷的加载后,该步载荷不予保留,去除后再加载下一步载荷。该模型下的边界条件是指在激光拼焊时,拼焊板和外围环境对流与辐射换热。
在激光拼焊过程中,焊缝区发生了液化,试样吸收大量的热量,在一次结晶时,试样又释放大量的热量,所以在计算温度场时不能忽略相变潜热对温度场的影响。
材料的热物理参数如比热容、导热系数等,在常温和高温条件下确定方法不一样,在常温下可以通过查阅相关文献获取;在高温条件下,就需根据实际情况利用插值法和外推法求出。创建三维瞬态温度场模块时,输出和输入参数都是通过矩阵来展现的。
专业从事机械产品设计│有限元分析│CAE分析│结构优化│技术服务与解决方案
杭州那泰科技有限公司
本文出自杭州那泰科技有限公司www.nataid.com,转载请注明出处和相关链接!